Pavements - Photometric Stereo Imaging (PSI)
Target of Investigation
Photometric stereo imaging is employed to detect surface cracks and surface textures of pavements.
Description
Unlike stereography, which uses two cameras, photometric stereo imaging uses a single camera and multiple light sources at fixed locations to determine local surface orientation (figure 1). The amount of light reflected by a surface is dependent on the orientation of the surface in relation to the light source and observer.(1) By having light sources at different angles, photometric stereo imaging produces images based on variations in shading of individual pixels. It also enables determination of surface orientation.
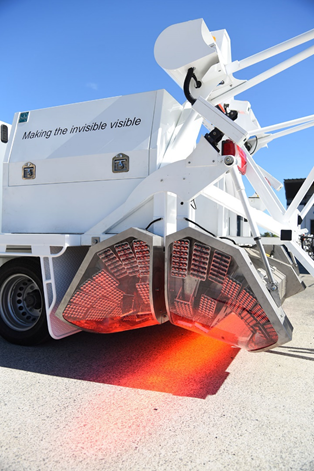
Physical Principle
As shown in figure 2, the surface normal at a local point is n. If the surface is diffusive, the surface albedo (k) is defined as the ratio of the reflection to the incident light.(3) Three illumination rays from different light sources are of unit vector intensity and in different planes.(4,5) The direction vectors are noted as l1, l2, and l3. Sources illuminate individually, and the light intensities observed by the camera are i1, i2, and i3 corresponding to l1, l2, and l3, respectively. The relationships between the observed intensities and the sources can be expressed by the equation in figure 3.
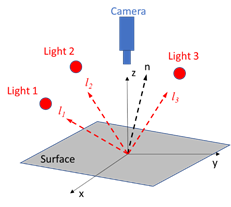
Figure 2. Illustration. Principle of photometric stereo imaging.

k is an assumed known value for pavement surface materials (asphalt or concrete). The observed intensities and directions of light sources can be obtained from the test. n can be solved for using the equation in figure 3. Figure 4 shows the matrix form of the equation in figure 3, and n can be solved for using the equation in figure 5. When there are more than three light sources, n can be solved for by making the least-squares errors in the equations, and the solution can be expressed in the matrix form shown in figure 6.(6) This model can also be extended to surfaces with nonuniform albedos.(7)

- Where:
- I = vector of the observed intensities.
- L = known 3-by-3 matrix of the normalized light directions.

Where L−1 is the inverse of L.

Where LT is transposed L.
Data Acquisition
The photometric stereo imaging system is usually integrated with a moving vehicle. Continuous imaging can be taken at highway speeds (100 km/hr [60 mph]), during which the photometric stereo imaging system will illuminate each light source in sequence at very high speeds.(8) A picture of the same area of the pavement surface is taken each time a light source is turned on. For example, a system with four light sources from different illumination angles will produce four images in sequence. The images will be captured by the charged coupled device of the camera and stored in the system’s computer for postprocessing.
Data Processing
Image processing is usually done by software, and the surface normalization is provided by the software as an image.
Data Interpretation
Cracks and different textures that cannot be seen in conventionally illuminated imagery can be seen directly in gradient maps generated from photometric stereo imaging (figure 7). Cracks are shown as lines and curves, and different textures are shown as grains of different sizes for different illumination combinations.
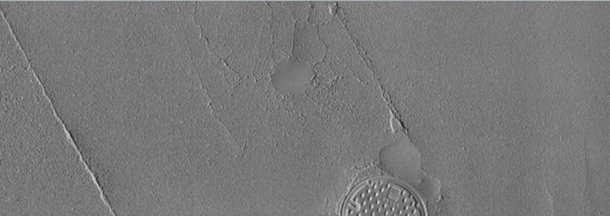
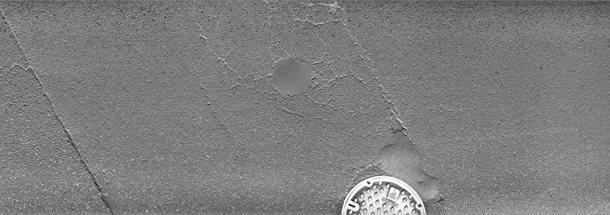
Advantages
Advantages of photometric stereo imaging include the following:
- Noncontact method.
- High accuracy in detecting surface cracks.
- Imaging at highway speeds.
Limitations
A limitation of photometric stereo imaging is the following:
- Cannot detect cracking when the surface is wet or covered by dirt or debris.
References
- Wu, Y. (n.d.). Radiometry, BRDF and Photometric Stereo, Northwestern University, Evanston, IL. Available online: http://users.eecs.northwestern.edu/~yingwu/teaching/EECS432/Notes/lighting.pdf, last accessed March 25, 2015.
- Earth Radar Pty Ltd. (2018). “Home.” (website) Yatala, Queensland. Available online: https://earthradar.com.au/, last accessed October 4, 2018.
- Woodham, R.J. (1980). “Photometric method for determining surface orientation from multiple images.” Optical Engineering, 19(1), pp. 139–144, SPIE, Bellingham, WA.
- Mathavan, S., Kamal, K., and Rahman, M. (2015). “A Review of Three-Dimensional Imaging Technologies for Pavement Distress Detection and Measurements.” IEEE Transactions on Intelligent Transportation Systems, 16(5), pp. 2,353–2,362, Institute of Electrical and Electronics Engineers, Piscataway, NJ.
- Pernkopf, F. and O’Leary, P. (2003). “Image acquisition techniques for automatic visual inspection of metallic surfaces.” NDT&E International, 36(8), pp. 609–617, Elsevier, Amsterdam, Netherlands.
- Verma, C.S. and Wu, M. (n.d.). “Photometric Stereo.” (website) University of Wisconsin, Madison, WI. Available online: http://pages.cs.wisc.edu/~csverma/CS766_09/Stereo/stereo.html, last accessed March 24, 2015.
- Barsky, S. and Petrou, M. (2003). “The 4-source photometric stereo technique for 3‑dimensional surfaces in the presence of highlights and shadows.” Transactions on Pattern Analysis and Machine Intelligence, 25(10), pp. 1,239–1,252, Institute of Electrical and Electronics Engineers, Piscataway, NJ.
- Reeves, B. (2010). High speed photometric stereo pavement scanner, US20130076871A1.