Pavements - Iowa Vacuum Joint Seal Tester (IA-VAC)
Target of Investigation
The Iowa vacuum joint seal tester (IA-VAC) is employed to test joint seals in concrete pavement for failure.
Description
Infiltration of surface water can contribute to the pumping of fines and subgrade or subbase softening or erosion. These issues can result in loss of structural support, pavement settlement, and faulting.(1–3) Joint sealants are used to minimize infiltration of surface water and incompressible materials into a joint system.(4,5) Joint sealants can also decrease the potential for dowel corrosion by reducing the penetration of deicing chemicals.(6) Testing the effectiveness of sealants with the IA-VAC can help diagnose sealant failures so measures can be taken to stop development of joint problems.
Physical Principle
The IA-VAC has a chamber that is 121.9 cm (48 inches) long by 15.2 cm (6 inches) wide. It is filled with soap and water and uses a vacuum pump to apply a vacuum pressure of less than 69 kPa (10 psi) to a joint seal that has been sprayed with a soap–water solution (figure 1). Any unsealed area along the joint will produce soap bubbles after the vacuum pressure is applied (figure 2).(7) The leakage location is recorded after testing (figure 3).
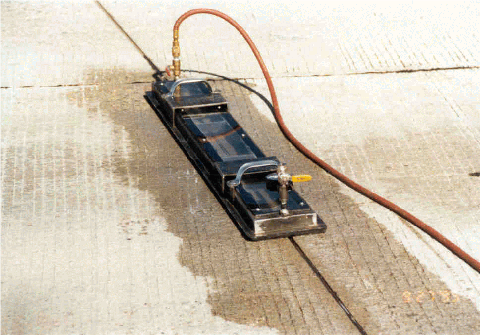
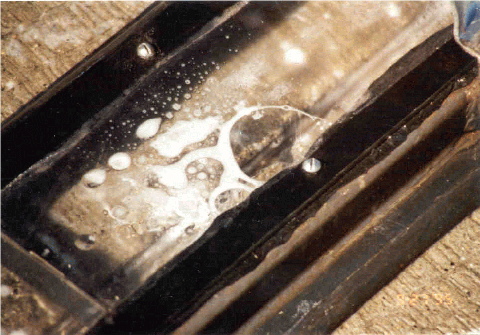
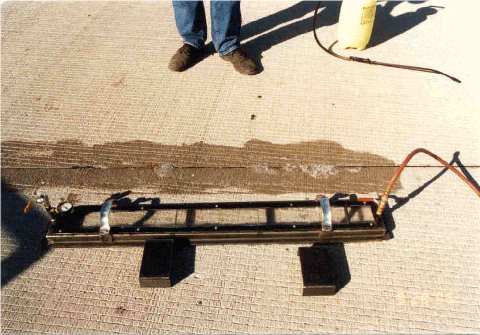
Data Acquisition
The following test procedure has been proposed by Purvis:(8)
- Select the test location
- Wet the area of road to be covered by the test chamber with soap and water (double‑spray the sealed joint with soap and water).
- Place a short piece of impermeable foam under each end of the test chamber (if the joint seal is more than 3 mm (0.125 inches) lower than the road surface in the joint).
- Place the test chamber over the joint; compress the chamber onto the road surface by having the operator stand on it until a vacuum indication is seen.
- Record the test location, vacuum reading, and the number and causes of leaks.
- Close the vacuum line valve and then release the vacuum valve.
- Repeat this process at each test location.
Data Processing
No data processing is needed.
Data Interpretation
Data are usually presented in a tabular form. By analyzing the results from the IA-VAC tests, information on the number and types of leaks can be obtained.(9)
Advantages
Advantages of the IA-VAC include the following:
- Testing equipment is easy to use.
- Single testing (without double checking) is fast.
- Cost is low.
Limitations
Limitations of the IA-VAC include the following:
- Lane closure and traffic control may be needed.
- Types of joint sealant failure (adhesive or cohesive) cannot be differentiated.
- Further analysis of causes of sealant failures requires professional experts.
References
- Federal Highway Administration. (1987). “Field Inspection Guide for Restoration of Jointed Concrete Pavements, Report No. FHWA-DP-X02-X01, FHWA, Washington, DC.
- Ray, G.K. (1980). “Effect of Defective Joint Seals on Pavement Performance.” Transportation Research Record, 752, pp. 1–2, Transportation Research Board, Washington, DC.
- American Concrete Pavement Association. (1991). Subbases and Subgrades for Concrete Pavements, Technical Bulletin TB011.02P, ACPA, Skokie, IL.
- American Concrete Pavement Association. (1991). Design and Construction of Joints for Concrete Highways, Report No. IS061.01P, ACPA, Skokie, IL.
- Federal Highway Administration. (1990). “Resealing of Concrete Pavement Joints.” Pavement Rehabilitation Manual, FHWA, Washington, DC.
- American Concrete Pavement Association. (1995). Joint and Crack Sealing and Repair for Concrete Pavements, Technical Bulletin TB012P, ACPA, Skokie, IL.
- Richter, J.M. (1999). Evaluation of Silicone Joint Seal Versus Preformed Compression Joint Seal, Report No. ND 94-08, North Dakota Department of Transportation, Bismarck, ND.
- Purvis, R.L. (2003). “Bridge Deck Joint Performance.” NCHRP Synthesis 319, Transportation Research Board, Washington, DC.
- Steffes, R.F. (1993). Innovative Leak Test for Pavement Joint Seals, Report No. 930422, Iowa Department of Transportation, Ames, IA.