Tunnel - Half-Cell Potential (HCP)
Target of Investigation
Half-cell potential (HCP) testing detects the potential for active corrosion of reinforcing steel
in concrete.(1) HCP measurements can be used for in-service evaluation of reinforced concrete when an electrical connection to the reinforcing steel can be made.(2)
Description
HCP measurements are based on the coexistence of corroding areas (anodic half-cells) and noncorroding areas (cathodic half-cells). An HCP probe is electrically connected to a steel reinforcement in the concrete. Different probes are available, including copper–copper sulphate (Cu/CuSO4) rods and rolling electrodes, depending on the application. Rolling electrode probes are better suited for rapid scanning of large, horizontal areas.(3) A portable half-cell probe, usually a Cu/CuSO4 standard reference electrode, is placed on the surface of the concrete.(4) The difference in potential between the reinforcement and the reference electrode is measured; these measurements are taken in a grid pattern on the structure to generate a spatial distribution of the corrosion potential. The difference in potential changes with the changing corrosion state of the reinforcing steel; thus, the changes can be indicators of active corrosion of the reinforcement.(5)
HCP test equipment includes a high-impedance voltmeter or data recorder and Cu/CuSO4 (or similar) reference electrode (figure 1). The positive terminal of the voltmeter is connected to the reinforcing steel of the structure, and the negative terminal is connected to the reference cell.(5)
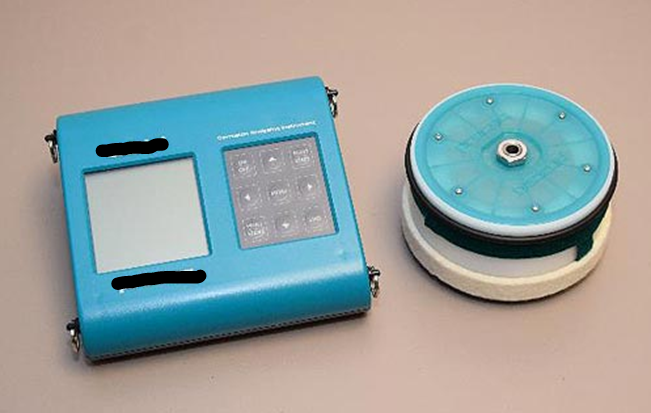
Figure 1. Photo. HCP data recorder and rolling electrode probe.(3)
This test cannot measure the degree of existing corrosion, and its effectiveness may depend on many factors.(3) For example, overlays, paint, and other coatings may prevent adequate electrical connectivity between the device and the concrete; protective coatings on the reinforcing steel will prevent adequate electrical connectivity between the steel and concrete.
When the surface of the concrete loses sufficient moisture, the concrete resistivity will be too high for the normal procedures, and specialized procedures may be required.(2)
Physical Principle
The corrosion of steel in concrete is similar to the electrochemical mechanism of the corrosion of a metal in an electrolyte. Separate anodic and cathodic processes take place simultaneously on the same metal surface. At the anodic site, iron is dissolved and then oxidized to iron ions, leaving electrons in the steel. At the cathodic site, oxygen is reduced, and hydroxyl ions are produced.(6) This electrochemical process generates an electrical field.(3) The potential of this field is measured using a high-impedance voltmeter and reference electrode, where the positive terminal of the voltmeter is connected to the reinforcing steel of the structure, and the negative terminal is connected to the reference electrode (figure 2). The reference electrode is usually galvanically connected to the concrete surface using a wet sponge.(6) The input impedance of the voltmeter should be in the range of 106 to 109 Ω.(6)
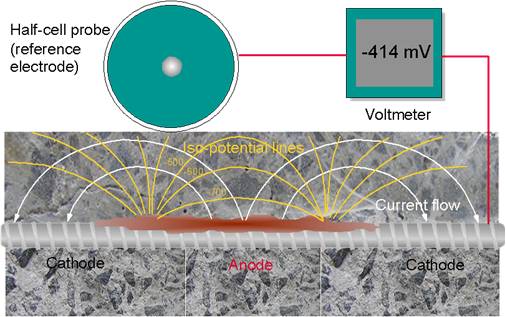
Note: Isopotential lines are measured in millivolts.
Figure 2. Illustration. Principle of HCP measurement.(4)
Data Acquisition
For data collection using HCP testing on concrete tunnel liners with uncoated rebars, the procedure described in ASTM C876-09, Standard Test Method for Corrosion Potentials of Uncoated Reinforcing Steel in Concrete, should be followed.(2) The following items are a summary of the data collection procedure:
- A grid for data collection should be laid out, ensuring points are not too close together so that redundant measurements are avoided and not too far apart so that localized corrosion is not missed. This grid will be dictated by the geometry, construction, and scope of the test area.
- The reinforcing steel is electrically connected to the positive lead of the voltmeter:
- The steel is located using a rebar locator, and a hole is drilled into it; a lead wire is connected to the steel using a self-tapping screw drilled into the rebar.
- All measurement locations should be electrically continuous with this screw.
- Multiple screws and corresponding measurement areas may be required to cover the entire survey area.
- The reference electrode is electrically connected to the negative lead of the voltmeter.
- The contact sponge of the reference electrode is wetted according to the following procedure to ensure good electrical contact with the concrete (prewetting can also be used if conditions allow):
- The entire surface or testing location should be wetted, but no free surface water should remain between test locations. A prewetted sponge is placed on each test location before measurements are taken and left in place for the duration of collection at that location.
- The reference electrode is placed on the test point, and the potential measurement is recorded (by hand or with the data acquisition instrument) after the voltage measurement has stabilized.
- The data collection procedure is repeated at the next test location; use of a rolling electrode probe allows the probe to remain in contact with the surface while moving from one test location to the next.
- After testing is complete, all tapped locations should be patched.
Data Processing
Typically, no processing of HCP data is performed, and the results are visualized as the measurements are taken.(6) Discrepancies in measurement accuracy may exist when there are extreme variations in the concrete cover depth, and HCP measurements may need to be adjusted based on measured deck electrical resistivity (ER) obtained at the same HCP test locations. Data are generally gridded and mapped using contour-mapping software based on the measured HCP data.
Data Interpretation
Data are plotted in a contour map using the spatial coordinates of the measurements to show areas with high probabilities of active corrosion of the reinforcing steel, low probabilities of active corrosion, and transition zones that span the measurements in between (figure 3).(4) HCP data should be interpreted by engineers or specialists experienced in corrosion activity and concrete materials. In addition to HCP data, other methods (chloride contents, ER, depth of carbonation, delamination surveys, rate of corrosion, environmental conditions) should be used to determine the corrosion activity of the embedded steel and its probable effect on the service life of the structure.(2) According to ASTM C876-09, areas with potentials greater than −200 mV have a 90-percent probability of no active corrosion, areas with potentials less than −350 mV have a 90-percent probability of active corrosion, and areas with potentials between these values have an uncertain probability of active corrosion.(2)
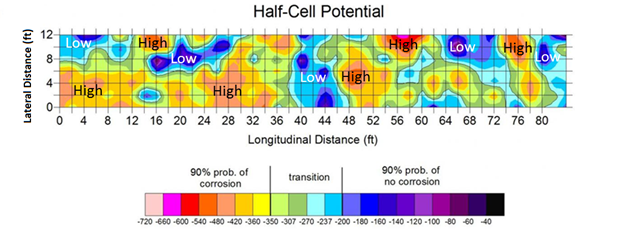
1 ft = 0.3 m.
Figure 3. Contour map. HCP measurements.(4)
Advantages
Advantages of HCP testing include the following:
- Rapid and easy to use.
- Effective over large areas.
- Minimal training required for data collection.
- Straightforward data processing.
Limitations
Limitations of HCP testing include the following:
- Interpreting results requires experienced personnel and correlation with other information to formulate conclusions about corrosion.
- Does not directly measure the corrosion rate of steel.
- Cannot be used with most overlays or coatings.
- Cannot be used with epoxy-coated reinforcing steel.
- Requires electrical connectivity to reinforcing steel throughout the test area.
References
- Marks, V.J. (1977). Detection of Steel Corrosion in Bridge Decks and Reinforced Concrete Pavement, Iowa Department of Transportation, Ames, IA.
- ASTM C876-15. (2015). “Standard Test Method for Corrosion Potentials of Uncoated Reinforcing Steel in Concrete.” Book of Standards 03.02, ASTM International, West Conshohocken, PA.
- Federal Highway Administration. (2016). “Nondestructive Evaluation Laboratory: Equipment.” (website) Washington, DC. Available online: https://highways.dot.gov/laboratories/nondestructive-evaluation-laboratory/nondestructive-evaluation-laboratory-overview, last accessed April 15, 2016.
- Gucunski, N., Imani, A., Romero, F., Nazarian, S., Yuan, D., Wiggenhauser, H., Shokouhi, P., Taffee, A., and Kutrubes, D. (2013). Nondestructive Testing to Identify Concrete Bridge Deck Deterioration, Report No. S2-R06A-RR-1, Transportation Research Board, Washington, DC.
- Boyd, S.R. and Frauss, P.D. (2006). Highway Concrete Technology Development and Testing: Volume V – Field Evaluation of Strategic Highway Research Program (SHRP) C206 Test Sites (Bridge Deck Overlays), Report No. FHWA-DR-02-086, Federal Highway Administration, Washington, DC.
- Gucunski, N., Romero, F., Kruschwitz, S., Feldmann, R., and Parvardeh, H. (2011). Comprehensive Bridge Deck Deterioration Mapping of Nine Bridges by Nondestructive Evaluation Technologies, Iowa Department of Transportation, Ames, IA.