Bridge - Dye Penetrant Testing (DPT)
Target of Investigation
The primary application of DPT for steel bridges is to detect and monitor cracks in steel bridge members, gusset plate connections, and welded details in the field. The technology relies on penetrant liquid being able to enter a crack and emerge at a later time due to capillary action. Consequently, subsurface cracks or volumetric weld defects (porosity, lack of fusion, slag inclusions, etc.) cannot be detected using DPT. Access is required to clean the surface, apply penetrant and developer, and visually observe results. Areas that are difficult to access or where other members interfere with access to the surface may be difficult to assess with DPT. Common field applications of the technology include detecting cracks at fatigue-prone details and verifying visual inspection results.
Description
Dye penetrant testing (DPT) is a nondestructive method for crack detection in metals. DPT is a process by which a liquid dye is applied to the surface to be inspected; this liquid dye seeps into cracks and other voids or depressions in the surface. The surface is then wiped clean, removing all of the dye from the surface. Dye that has penetrated into a crack is not removed by the cleaning and emerges from the crack due to capillary action. This results in a visible indication of the crack on the surface.(1,2)
To ensure that the indication is easy to observe visually, the color contrast between the liquid dye and the surface undergoing inspection may be enhanced. For typical field inspections of bridges, this is accomplished by applying a developer to the surface after it has been cleaned. Developers are typically white in color; the liquid dye is typically red. The color contrast between the white developer and the red dye ensures that crack indications will be easily observed by an inspector.
Another method of improving the contrast between an indication and the surface being inspected is to use fluorescent dye. A fluorescent dye contains particles that, when illuminated with ultraviolet light, emit intense visible spectrum light. This improves the light intensity contrast between the fluorescing dye crack indication, and the surface under inspection, which is not fluorescing. However, generally dark ambient light conditions (≤ 2 fc) are required to observe the light contrasts between the dye and the surface being inspected.(1,2) Consequently, fluorescent DPT is not commonly used for bridges in the field.
Physical Principle
DPT works on the physical principle of capillary action. Capillary action (or capillary motion) describes the ascension of a liquid along a surface in opposition to gravity. This occurs when the adhesive forces between a liquid and a solid surface exceeds the cohesive forces within the liquid itself. As a result, the liquid spreads along the solid surface and can overcome the gravitational forces to “climb” along the surface in a vertical direction. For DPT, liquid confined within a crack emerges to the surface of the material, forming an indication of the presence of the crack on the surface of the material.
Data Acquisition
Data acquisition for DPT consists of cleaning the surface to be inspected, applying a colored or fluorescent liquid penetrant, applying a developer to improve contrast, and then interpreting indications of the dye penetrant emerging through the developer. Figures 1 through 4 demonstrate several steps in the procedure. The procedure begins with cleaning the surface of the material to remove coating and any debris and foreign material from the area to be assessed. Once the surface has been fully cleaned, a colored dye penetrant is applied in a thin coating on the surface (figure 1). The colored dye is allowed to rest on the surface for a “dwell” period lasting 10 to 30 minutes. This dwell period allows the dye to penetrate any discontinuities in the surface, e.g. cracks. Once the desired dwell time has passed, the surface is thoroughly cleaned with a cloth moistened with solvent to remove all dye from the surface (figure 2). Developer is then applied to the surface in a thin, even coat (figure 3). The developer is typically a white powdery coating that covers the surface and dries quickly. An additional dwell time of 5-15 minutes allows the penetrant the time necessary to emerge from cracks in the surface and form an indication on the surface of the material (figure 4).
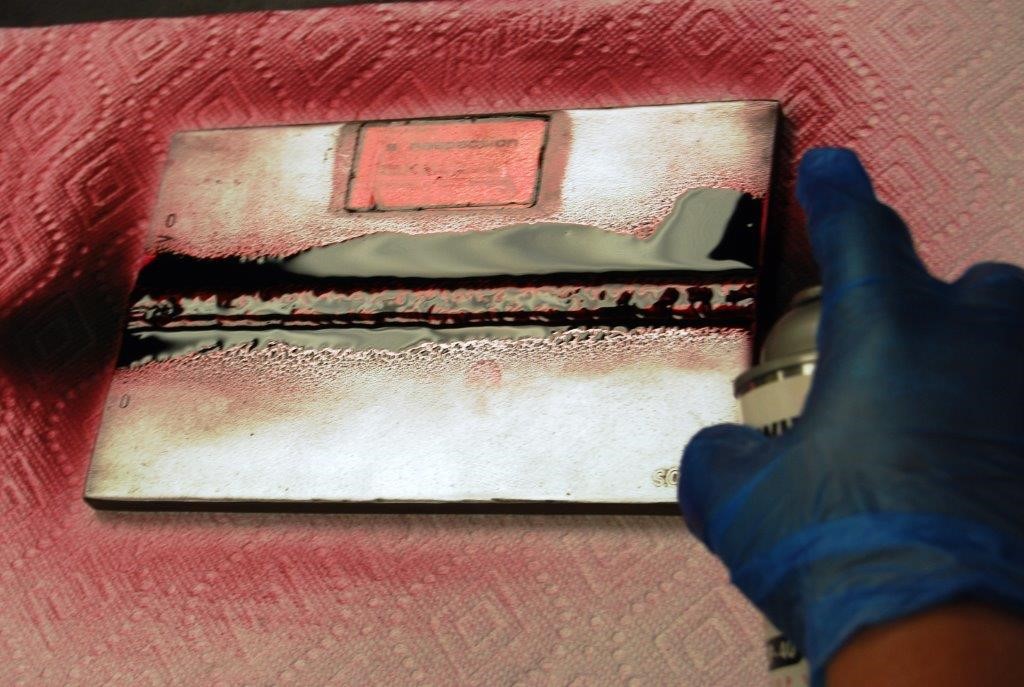
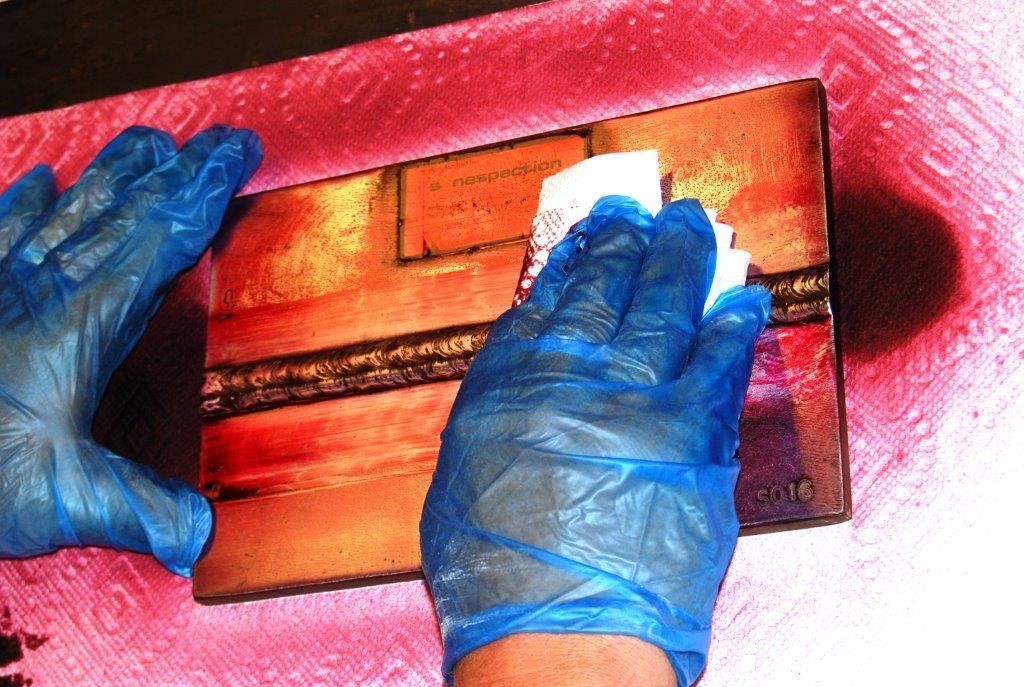
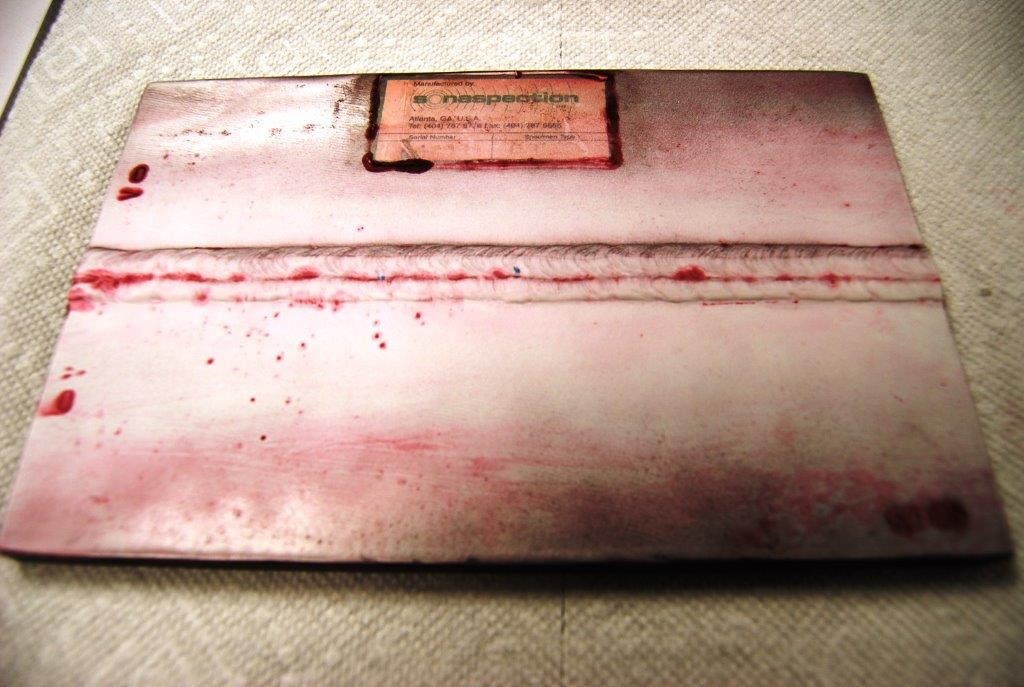
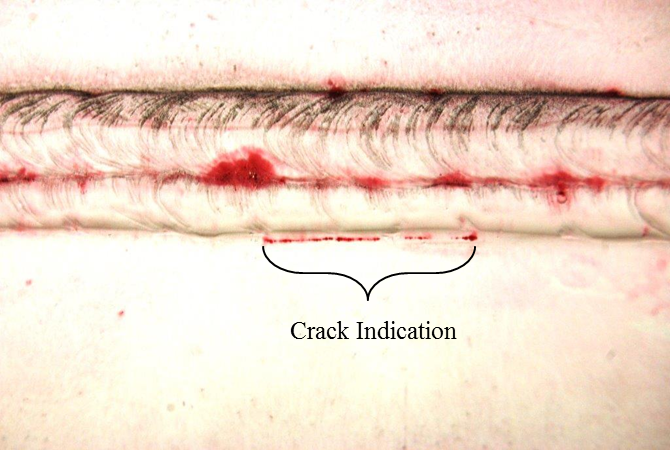
Data Processing
The data produced from a DPT inspection are visible indications on the surface of the material being tested. Indications are photographed and documented by notes or on an inspection report.
Data Interpretation
Data interpretation consists of visual observations of penetrant emerging from features on the surface of the material. Linear indications are generally interpreted as indicating cracks. Non-relevant indications are produced when dye becomes entrapped in a surface feature that is not a crack and emerges through the developer. Inadequate surface cleaning can result in non-relevant indications, as dye emerges from debris on the surface or from under coatings that have not been fully removed. Welds with surface relief due to undercut, surface porosity, or a rough weld bead may also produce non-relevant indications.
Advantages
- Simple to apply, minimal training required.
- Relatively easy data interpretation.
- Low cost.
- Materials can be stored on inspection vehicle for later use.
Limitations
- Requires removing all coatings, compromising corrosion protection.
- Requires extensive surface preparation, potentially producing hazardous materials when lead paints are present.
- Requires long time intervals to apply (~30-60 minutes).
- Long dwell times (~10 minutes for penetrant to seep into cracks, and ~10 minutes for penetrant to appear through developer).
- Detects only surface-breaking cracks.
References
- ASTM, “Standard Practice for Liquid Penetrant Testing,” E1417-11, West Conshohocken, PA, 2011.
- ASTM, “Standard Practice for Liquid Penetrant Examination for General Industry,” E165-12, West Conshohocken, PA, 2012.